What material should you use in your next build?
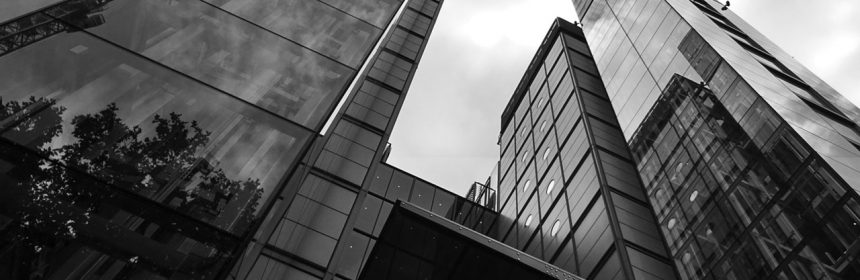
Before modern technology and the ability to control steel and concrete, the area of architecture consisted of wood and cave dwellings. We have come a long way since then, in terms of having the choice to build with many different materials. Today’s cities show skies punctuated by buildings so tall even architectural tour guides encounter the occasional pain in the throat. So, which substance reigns supreme in the area of development today? Should we be using metal fabrication such as steel, or concrete in your next build? Both provide numerous advantages, yet different materials cater for your various needs.
Safety
The building’s center (where lifts, stairs, and electricity systems are located) will be encased in 2-foot-thick concrete for security in case of a fire or terrorist attack in extreme situations. Cast-in-place reinforced concrete provides outstanding resistance to burst and/or impact. This being said, concrete requires no extra fireproofing treatments to fulfill stringent fire codes and performs well during both the natural and man made disasters. Due to concretes inherent heaviness, mass, and strength, buildings constructed with cast-in-place reinforced concrete can withstand winds of over 200 mph and perform well even under the impact of flying debris, giving this material a popular stance due to its structural ability.
With good design, engineering, wire fabrication, and construction, the rigid structures constructed with concrete can exhibit greater ductility, which is a must in areas prone to seismic activity. However, with the inclusion of passive fire protection such as spray-on fireproofing, buildings constructed of structural steel may sustain greater temperatures and, thus, provide additional security.
Do not base your opinions about steel’s performance on the occasions of accidents or unfortunate events. The report indicates that the inherent redundancy of the steel frames averted the structure’s collapse. We’re seeing plenty of structures built taking into consideration progressive collapse for burst conditions that have been designed very efficiently and very efficiently in steel.
Cost
It is true, costs of building materials have spiked. However, the price of ready-mix concrete stays relatively steady and even the growth in steel has had a minimal impact on reinforced concrete construction projects. Concrete costs remain very stable despite the varying and significant increases in additional construction material costs.
Whilst cast-in-place concrete structure can be more expensive on the front end, the return on investment achieved can decrease the cost differential. Insurance companies recognize the advantages of a cast-in-place reinforced concrete office building since the above benefits; enhanced safety and structural integrity and to decrease accountability on their part. Some insurance companies claim that developers and owners of reinforced concrete-framed office towers with a concrete core, and broader egress stairs, will save almost 25 percent annually on the cost of property insurance.
The big news in evolution is the amount of steel. And while structural steel has undergone a 50-percent rise over mill costs since November 2003, specialists such as cross stress that structural steel represents less than 20 percent of all of the steel used in building construction. If you examine the overall effect on project costs, in the past year we have seen job costs go up by about 10 percent because of gains in all kinds of construction materials.
And despite what some concrete specialists say, in the event that you thought you would escape the rising steel costs by opting for reinforced concrete, then consider again. The costs to get a concrete framing system have gone up quite much equivalently into the expenses of a steel and wire framing system. For a precise reading on which material is most cost effective, analyze current concrete and steel framing costs on a project-by-project foundation.